In the burgeoning industrial landscape, the cardinal role of professionals involved in quality assurance continues to rise in significance. Rooted in their pursuit are the twin objectives of enhancing consumer satisfaction and maintaining superior standards of product or service deliverance. This exploration aims to unpack the myriad facets of a career in quality assurance, starting from understanding the functioning of these professionals across varied sectors to dissecting the methodologies and tools employed on the frontline. Furthermore, an eye will be kept on the advancement opportunities in this line of work while addressing the typical challenges that present themselves and suggesting feasible methods to navigate around them effectively.
Understanding the Role of a Quality Assurance Professional
Role and Responsibilities of a Quality Assurance Professional
A Quality Assurance (QA) professional, also sometimes referred to as a Quality Assurance Engineer or QA Tester, plays a crucial role in ensuring that the products or services offered by a company meet the required quality standards. The primary responsibility of a QA professional is to enforce quality standards by conducting rigorous testing and meticulous inspection of products or services.
On a regular basis, the QA professional would develop test plans and procedures based on the defined quality standards. They would then conduct testing according to these plans, documenting and reporting any issues or defects they uncover. This role demands a keen eye for detail as they need to spot flaws that others might overlook.
Aside from physically testing products or services, QA professionals also review system requirements and track quality assurance metrics such as defect densities and open defect counts. They also review and analyse the effectiveness of QA processes and make recommendations for improvements.
In industries like manufacturing and food production, QA professionals may also be involved in product recalls, dealing with noncompliance issues, and developing corrective action plans. They liaise with external bodies and inspectors to ensure conformity with legal standards and regulations.
Skills Needed to Excel in Quality Assurance Jobs
The skills required for a QA job vary depending on the nature of the industry. However, there are certain universal skills that can help a QA professional excel in their role.
Attention to detail is paramount, as QA professionals are expected to spot errors or anomalies which might not be obvious. Strong problem-solving skills are also essential as they often need to identify the root cause of defects and suggest improvements.
A good understanding of various testing tools and methodologies, as well as knowledge of quality assurance standards and regulations is a crucial part of a Quality Assurance job. Some industries may require QA professionals to be familiar with specific coding languages or technologies.
Analytical skills are a must, as interpreting and understanding complex data forms a significant part of this role. Strong written and verbal communication skills are also necessary, as these professionals often need to liaise with different teams within the organisation and even external regulators.
The Significance of Quality Assurance Across Various Sectors
Quality Assurance is a pivotal facet across all sectors, such as software development, manufacturing, pharmaceutical, and the food industry. Its primary role is to certify that the products manufactured are dependable, secure, and produced to an elevated standard.
With relation to industries like food production or pharmaceuticals, where the quality of a product can lead to substantial health and safety implications, it’s the QA professionals who make sure the products are up to the rigorous safety and quality guidelines. Consequently, they perform a crucial function in safeguarding consumers.
In the IT and software industry, QA professionals are held accountable for the functionality of software and applications as per the requirement, thereby escalating user experience and fulfilling client necessities. They help to discover and fix glitches in the early stages which aids in cost and time reduction, and sustains a company’s standing and reliability.
As far as the manufacturing sector is concerned, proficient Quality Assurance results in a decrement in product defects, leading to a decrease in manufacturing expenses and wastage, customer contentment and fidelity enhancement, and superior gains in the end.
Thus, Quality Assurance is instrumental in maintaining product caliber and accomplishing customer satisfaction. It aids in instilling trust between a company and its customers by ensuring uniformity and dependability.
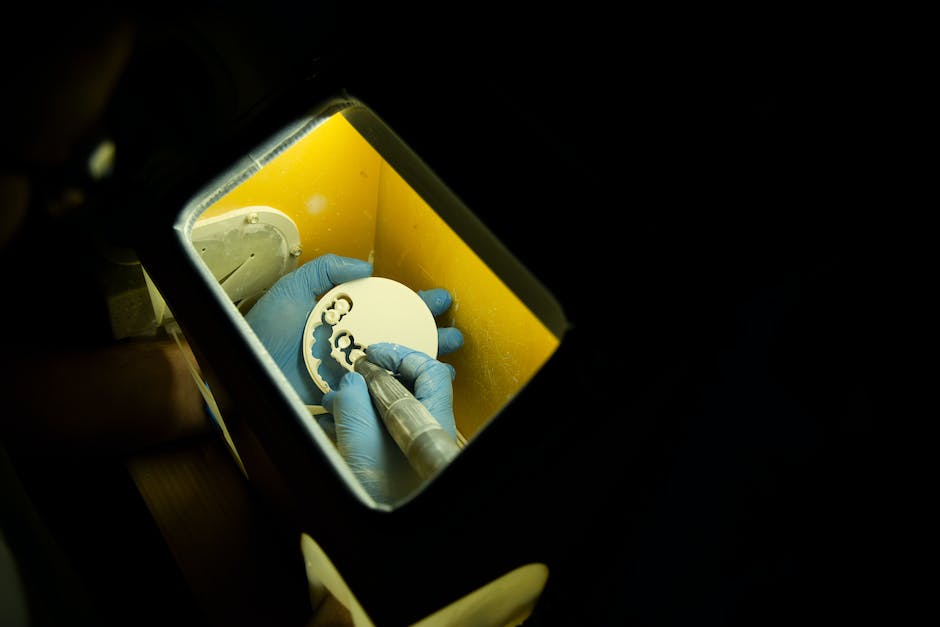
Quality Assurance Methodologies and Practices
A Closer Look at Quality Assurance
Quality Assurance (QA) encompasses a systematic process that involves established guidelines and tasks to produce products or services complying to specific quality standards. These standards are ordinarily set out by the industry, but in certain cases can also be dictated by governmental or regulatory bodies. Quality assurance accommodates a diverse range of products or services, from software conception to the manufacturing of tangible products.
Quality Assurance Methodologies
There are several quality assurance methodologies and frameworks used by businesses to achieve and maintain high-quality standards. These include Six Sigma, Lean manufacturing, and Total Quality Management (TQM).
Six Sigma
Six Sigma is a data-driven methodology focused on eliminating defects and reducing process variability. It seeks to improve overall output quality by identifying and removing the causes of defects and minimising variability in manufacturing and business processes. It uses statistical methods to measure and improve a company’s operational performance, practices, and systems. The term ‘six sigma’ comes from its goal, which is to enable processes to produce results with no more than 3.4 defects per million opportunities.
Lean Manufacturing
Alternatively, Lean manufacturing, or simply Lean, is a methodology that focuses on eliminating waste within processes and continuously improving the process flow. Waste in this context refers to any activity or input that does not add value to the final product or service from the perspective of the customer. Lean methods can increase productivity, reduce costs, and improve overall quality of products or services.
Total Quality Management
Total Quality Management (TQM) is a comprehensive and structured approach to organisational management that seeks to improve the quality of products and services through ongoing refinements in response to continuous feedback. TQM requirements may be defined separately for a particular company or may be adhered to standards such as the International Organization for Standardization’s ISO 9000 series. TQM endeavours to deliver high-quality products and services through customer satisfaction with continuous feedback.
Applying Quality Assurance Methodologies to Jobs
In relation to quality assurance roles, understanding and implementing these methodologies are key job requirements. Quality assurance managers, engineers, or analysts implement these methodologies to ensure products or services meet established quality standards. They might design and implement tests, inspect production operations, identify and record defects, track and analyse defect patterns, and implement corrective actions when necessary. These job roles require a solid understanding of various QA methodologies to drive process improvements and deliver quality results consistently.
Quality Assurance’s Role in Enhancing Products and Services
Quality assurance methodologies have the capacity to bestow a wealth of advantages onto a business’s products or services. Primarily, they allow an organisation to consistently produce high-quality goods or services, but these methodologies also offer other competitive benefits. These include bolstered customer satisfaction, decreased operational costs, a broader market share, and an enhanced reputation. Effectively deploying these methodologies within quality assurance positions fosters a cycle of continuous improvement in product and service quality.
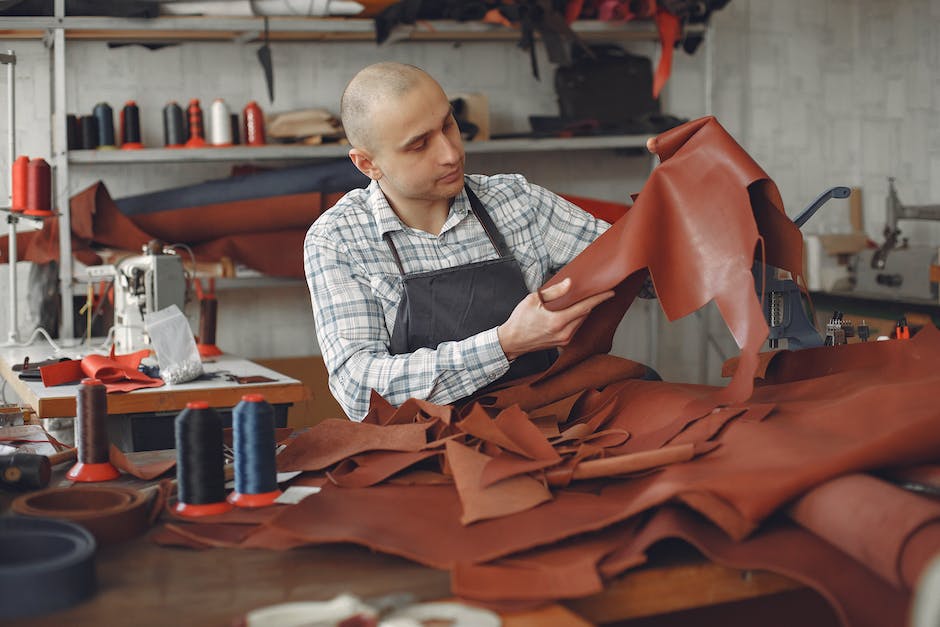
Quality Assurance Tools and Technologies
Comprehension of Tools and Technologies Essential to Quality Assurance
Understanding the tools and technologies pivotal to quality assurance form an integral component of industry-wide quality management procedures. These provisions play a vital role in the control of errors, refinement of processes, and enforcement of the quality standards set for end products or services. Grasping these tools and technologies deeply is paramount to superior quality control.
Generally, these tools and technologies can be divided into a few unique categories: software testing tools, issue tracking tools, and performance testing tools. Software testing resources, such as Selenium, Katalon Studio, and TestComplete allow for the identification and resolution of system faults before software deployment, ensuring that the software functions as intended across versatile environments and situations.
Issue tracking tools, or bug tracking tools, enable the detection, monitoring, and management of bugs or problems that may surface during the software development cycle. Examples include JIRA, Bugzilla, and Mantis. By providing a coherent strategy to address bugs or problems, these tools promote a smoother software development lifecycle, ultimately resulting in higher quality products.
Performance testing resources, like Apache JMeter and LoadRunner, scrutinize the software’s speed, response time, and stability under a variety of workload circumstances. They offer insights into the software’s behaviour and highlight potential scalability concerns.
Furthermore, recent advancements in quality assurance technologies have introduced automated testing tools like UFT (Unified Functional Testing) and Test Complete. These not only streamline and remove human error from the testing process but also enhance test coverage and accuracy which, in turn, guarantees a superior level of quality assurance.
Mastery of Quality Assurance Tools
Gaining proficiency in employing quality assurance tools can considerably enhance your QA efforts. For instance, it is of paramount importance to identify and use software testing tools that are best suited to the specific needs of a project. Additionally, an in-depth understanding of these tools can expedite the process of testing and rectifying software.
Issue tracking mechanisms should be put in place from the outset of the software development cycle. This ensures that any emerging issues are promptly identified and dealt with, thereby preventing them from ballooning into more significant challenges.
One must also utilise performance testing tools both during and after the development stage to verify the software’s capability to withstand high traffic loads.
In summary, these quality assurance tools and technologies play a critical role in maintaining product or service quality, fostering higher customer satisfaction and driving business success. Therefore, developing expertise in the integrated use of these tools can significantly amplify one’s potential in a quality assurance role.
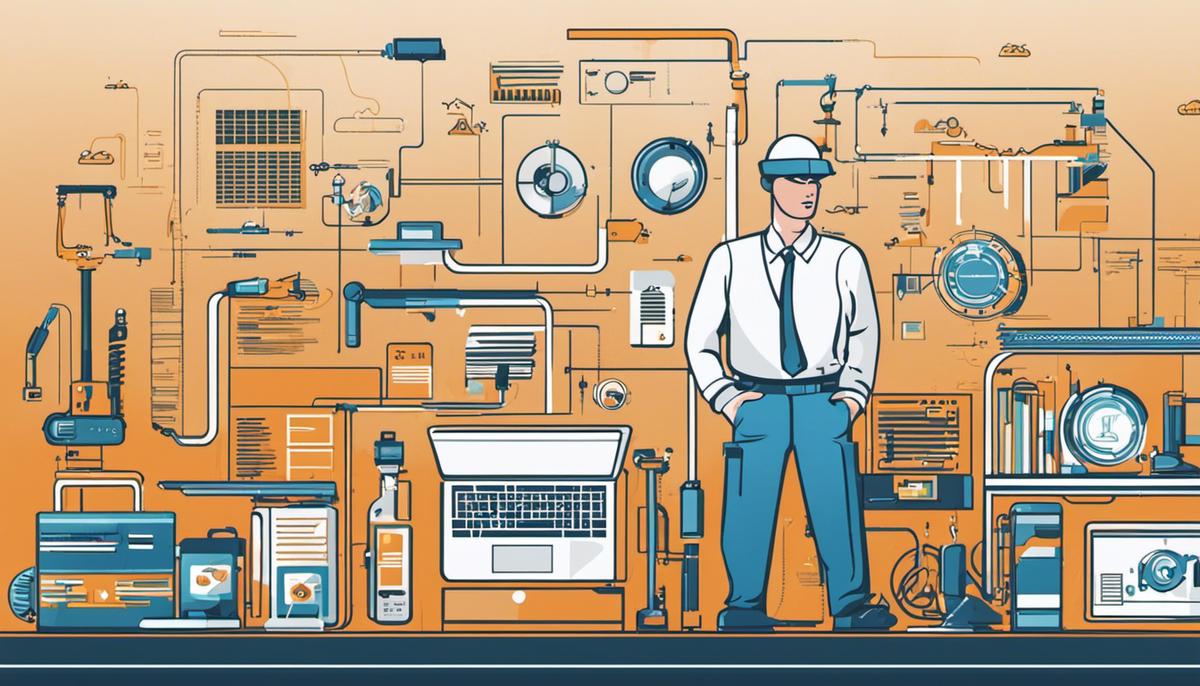
Career Prospects in Quality Assurance
Quality Assurance (QA) is a critical component across a wide range of industries, including software development, manufacturing, retail among others. The primary responsibility of QA professionals is to ensure that a product or service aligns with stipulated specifications and exhibits unwavering quality. Their role is crucial in upholding the company’s reputation, enhancing customer satisfaction, and bolstering profitability. QA encapsulates methodical activities such as inspections, audits, and testing, all aimed at determining whether a product or service meets established parameters.
The career path of a QA professional varies according to the industry. In software development, professionals can start as Quality Assurance Engineers or Testers, then move into roles like Lead QA Engineer, QA Team Coordinator, and eventually QA Manager or Director. They may also have the opportunity to diversify into specialised roles like Automation Test Engineer or Performance Test Engineer.
In manufacturing or pharmaceutical industries, QA professionals usually begin their journey as QA Inspectors or Technicians. With time and experience, they can progress to QA Analysts, QA Engineers, QA Managers, or Quality Control Managers. A deep understanding of industry-specific Certification bodies’ regulatory guidelines (like ISO in manufacturing or FDA in pharmaceuticals) is key to success in such roles.
The field of quality assurance offers substantial opportunities for professional growth. Demonstrating competency, gaining industry-specific certifications and actively updating one’s skill set can hasten career progression. Specific certifications like Certified Quality Engineer, Certified Manager of Quality/Organizational Excellence, or Certified Software Quality Engineer can enhance employability and confer a competitive edge.
QA Managers often move into roles that effect strategic quality decisions like Director of Quality, VP of Quality, or even Chief Quality Officer, particularly in larger organisations where quality holds a central role. Alternatively, many QA professionals expand their skill set to venture into related areas such as project management or operations management.
The average earnings for QA professionals can significantly vary depending on the industry, geographical location, and individual skill set. In the UK, a Quality Assurance Engineer can expect an average salary of around £35,000 per year, while Lead QA Engineers can make approximately £55,000 per annum.
Quality Assurance Managers see a more substantial wage with an average salary in the region of £53,000. But in high-demand sectors (aviation, pharmaceuticals, and software development) or in multinational companies, QA Managers salaries can easily exceed £70,000. At the highest echelons, Directors of Quality and VP of Quality roles can command six-figure salaries, influenced by factors like organisation size, complexity, and geographic location.
A role within Quality Assurance (QA) is far more than the identification and rectification of faults. It is about the creation of a culture whereby continuous improvement is encouraged and seen as a key business strategy. There appears to be a promising future for those within QA roles, with an escalating demand for such professionals. The avenue for career progression and the potential to earn well make QA an appealing career path.
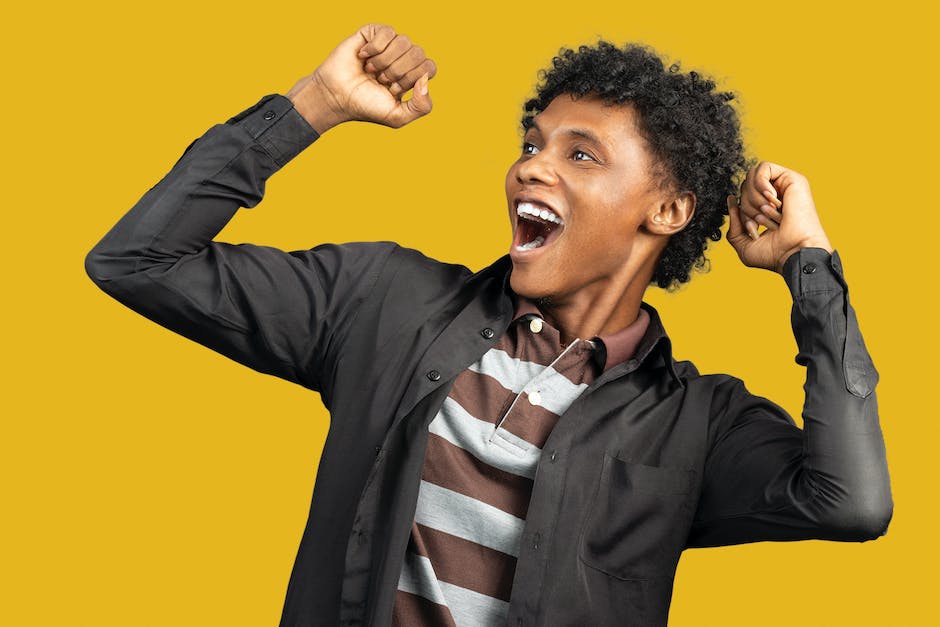
Challenges in Quality Assurance and Ways to Overcome Them
The Complexities of a Quality Assurance Role
The role of a quality assurance professional is to ensure that products or services meet the desired levels of quality. These specialists endeavour to prevent any mistakes or faults in the manufacturing process and to foresee any future issues that could arise when solutions are delivered to clients. However, this crucial role does come with its own unique set of complications.
Pace and Pressure to Deliver
In today’s fast-paced and ever-evolving business environment, one of the main challenges QA professionals face is the speed and pressure to deliver. As businesses strive to stay competitive, the time allocated for QA processes is often squeezed. This can lead to oversights and rushed inspections, resulting in a failure to identify issues that may affect the quality of the product or service.
Complexity of Tasks
The increasing complexity and sophistication of products and services create challenges for quality assurance personnel. They have to navigate complex systems, processes, and ever-evolving production technologies. Grappling with these intricate facets can be daunting and require an ongoing commitment to training and skill development.
Changing Quality Standards
Another challenge encountered is the ever-changing standards and regulations. Keeping up with industry standards, statutory requirements, and customers’ changing expectations adds layers of complexity to a QA specialist’s job. Sometimes, these standards and regulations can conflict, creating a predicament for the quality assurance professional.
Ways to Overcome These Challenges
To overcome these challenges, strategies and solutions need to be employed. One key method is investing in robust, state-of-the-art testing and inspection tools. Technologies like AI and automation have the potential for real-time monitoring of production processes and can quickly identify anomalies that need to be addressed.
Dealing with the fast-paced nature of business today calls for lean and agile approaches to QA. Adopting iterative feedback loops, where potential issues are identified early in the production process, can go a long way towards ensuring quality while maintaining delivery schedules.
To handle the complexity of tasks, continual education and training are essential. Regular in-house training sessions, professional certifications, and workshops can equip QA personnel with the latest skills, knowledge, and best practices.
Lastly, in dealing with ever-changing standards and regulations, QA specialists need to proactively engage with regulatory bodies, industry thought leaders, and customers. This proactive engagement can provide early insights into upcoming changes and help strategise the necessary course of action.
By focusing on these strategies, quality assurance professionals can deftly navigate the obstacles they face, ensuring that they reliably keep the quality promise to their customers.
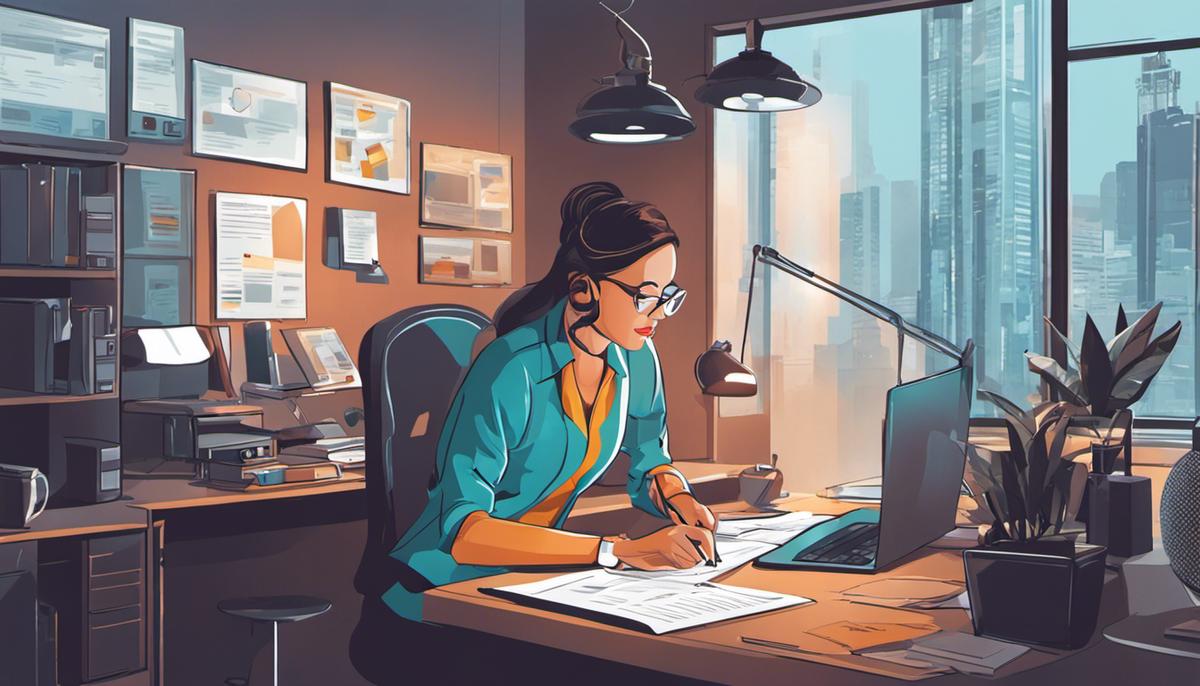
Quality assurance is known to form the backbone of industrial success, and its efficacy underscores the smooth running of operations within an organisation. It is imperative for professionals stepping into this field to comprehend the methodologies and tools which continue to evolve over time. While there are definite career prospects, one must be prepared to face and overcome an array of challenges that come with the territory. Ultimately, the key to a successful career in quality assurance lies in the fine balance between learning, adapting, and innovating for continual improvement of the product/service quality landscape.